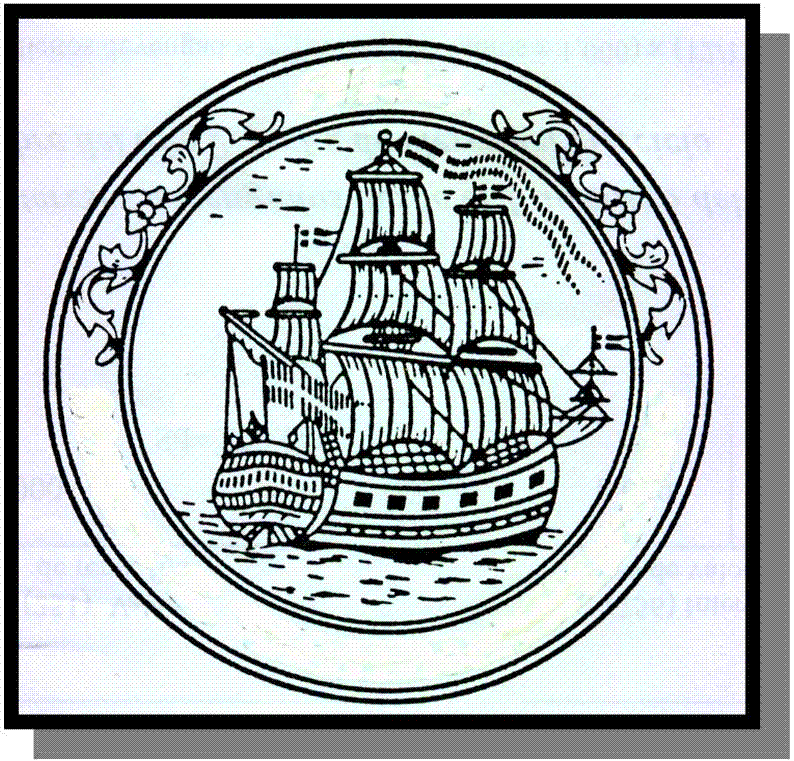
INTERNATIONAL SHIP´S REGISTER
VETTING INSPECTIONS
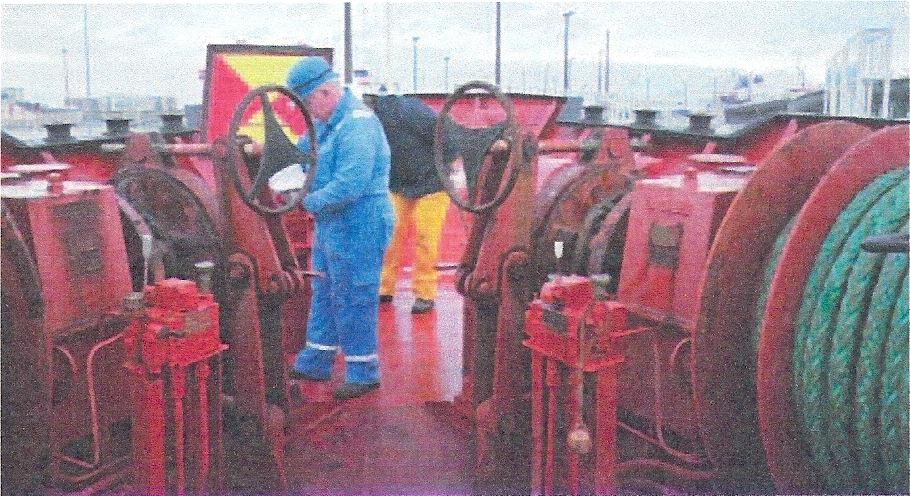
Company Profile
I.S.R. consultants provide ship vetting support to oil tradig companies and their
vetting auditors to ensure proper inspection of vessels in Spain and the Canary
Islands.
The following services are offered:
1. Coordination of ship inspection arrangements and scheduling.
2. Liason between oil trading companies and regional shipping
companies or any other body as designated.
3. Follow up with shipping companies regarding the progress of
the Owner´s response and status of the ship inspection.
4. Accommodation arrangements for vetting inspectors arriving
for ship inspection.
5. Arrangement of transportation for inspectors to the Spanish
ports and berths.
I.S.R. technical personnel monitor the operation, maintenance, performance and
procedures of each vessel. They work in collaboration with the ship´s management
team to ensure each nominated vessel meets the principal´s expectations, and all
industrial standards. Timely monitoring and reporting is achieved throug strict
implementation of Quality Assurance procedures with regular hands-on inspections,
and the incorporation of innovative marine practices.
The vessel vetting inspectors use the industry-agreed Oil Companies International
Marine Forum (OCIMF) SIRE inspection format as the main ship inspection criteria.
All questions are carefully answered to make the report useful to other SIRE
participants who may wish to access the report at a later date. Inspectors detail
both positive and negative aspects of the ship´s operations during the inspection.
Ships are assessed using international conventions and industry recommendations
such as the Inert Gas System (IGS), Safety of Life at Sea (SOLAS), and the
International Convention for the Preventing of Pollution from Ships (MARPOL).
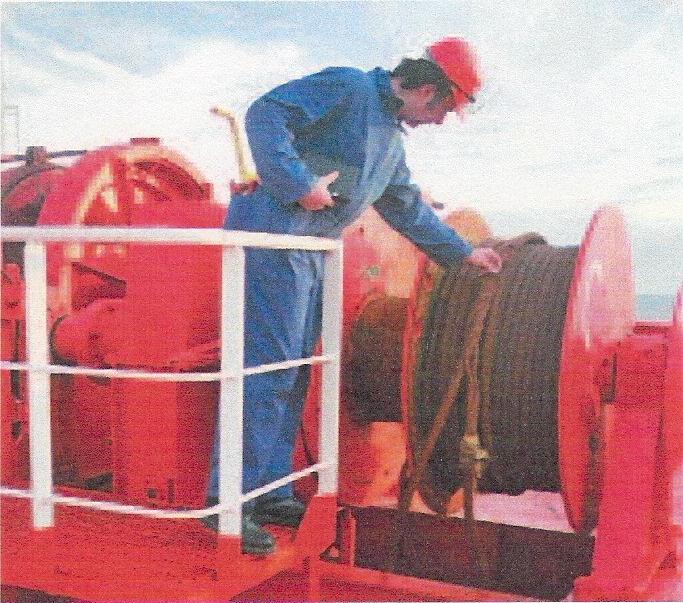
Guidance provided by the International Safety Guide for Oil Tankers and Terminals
(ISGOTT) pertains to all tanker types and the Society of International Gas Tankers.
However, a "high risk" observation list is utilized to identify items of greater
concern.
Inspectors are required to report all vessel or operational deficiencies in their reports.
Any deficiencies found to be serious are assessed as "high risk", and identified as such
on an Observation List left with the ship´s Master at the end of each inspection. The
use of such vessels is precluded until all observations have been satisfactorily closed
out, with special emphasis placed on those items assessed as "high risk".
Following the succesful close uut of an inspection report, the ship Owner is advised
that further operational inspection may not be required for a period of time. This
does not constitute a blanket approval of the vessel for business, and the vessel are
screened each time they are tendered for business.
Generally, at the beginning of the audit, the ship inspector is accompanied by an
I.S.R. representative to meet with the Captain. They discuss the vessel´s schedule
and inspect the vessel with care, as to not interference with the cargo work.
It is recommended that they are accompanied by a senior officer of the relevant
department - i.e. the Master or Chief Engineer.
It is helpful if the vessel has prepared the initial paper work, shuch as all the trading
certificates, crew certificates, etc. It is a good idea to keep all files, log books and
other records ready in the ship´s office prior to the inspector´s arrival. In addition to
being convenient during the documentationn review, it also creates a positive
impression regarding the professionalism and foresight of the vessel´s officers.
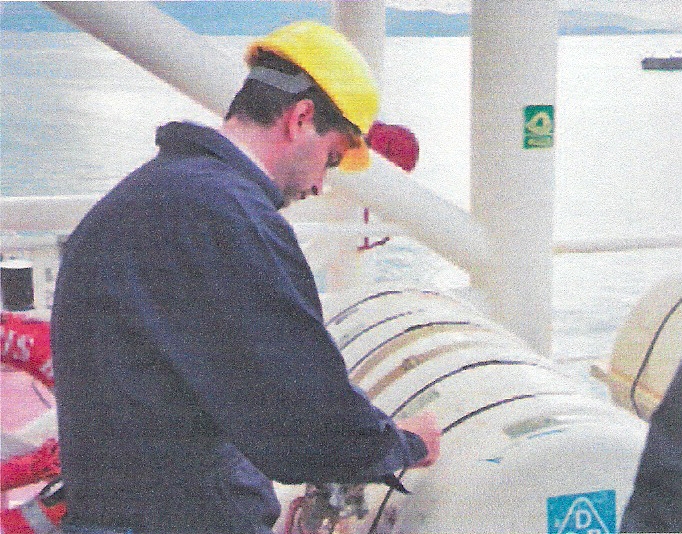
The audit team reviews the following, where applicable:
1. Certificate of Registry.
2. The vessel´s trading Certificates: Safety Equipment, Load Line, Safety Radio,
IOPP, Safety Construction, International Tonnage, ISM Document of Compliance
(certified copy), ISM Safety Management Certificate, Certificate of Fitness or
Noxious Liquids Certificate.
3. Oil Record Books, Parts 1 and 2 or Cargo Record Book.
4. Certificates of Civil Liability for Oil Pollution.
5. The Certificate of Financial Responsibility and the last Tank Vessel Examination
letter.
6. The Class Certificate, Enhanced Survey File with Condition Assessment Report
and Quaterly Class Reports.
7. Approved manuals: Stability, Damage Stability, Inert Gas, COW, CBT, and ODME.
8. An approved SOPED and VRP Manual.
9. SOLAS Training Manual, SOLAS Maintenance Manual, life saving appliance and
fire fighting equipment maintenance records.
10. The Procedures and Arrangements Manual (for chemical and gas carriers).
11. The Cargo Gear Register.
12. Officer and Crew National Certificates of Competency, Continued Proficiency
and Dangerous Cargo Endorsements.
13. Evidence of Administration acceptance of Crew Certificates of Competency.
14. The Manager´s Operating Instructions.
15. The Company Drug and Alcohol Police and records of unannounced testing.
16. The Garbage Record Book and the Garbage Management Plan.
17. Records of testing of mooring winch brakes, mooring rope/wire manufacturer´s
certificates, bow stopper certificate.
18. The last Port State Inspection certificate.
19. Hot work and enclosed space entry permits.
20. The technical publications listed in the OCIMF Vessel Inspection Questionnaire
as applicable to the vessel.
Once the paper work has been completed, the audit team makes their way around the deck
to identify any deficiencies, and may also ask the crew members a few questions. On
completion of the deck round, they go down to inspect the Engine Room. It should be noted
that the Emergency Fire Pump, Emergency Generator, Emergency Steering and the ODME
are expected to be operated by the officer or any other representative accompanying the
audit team.
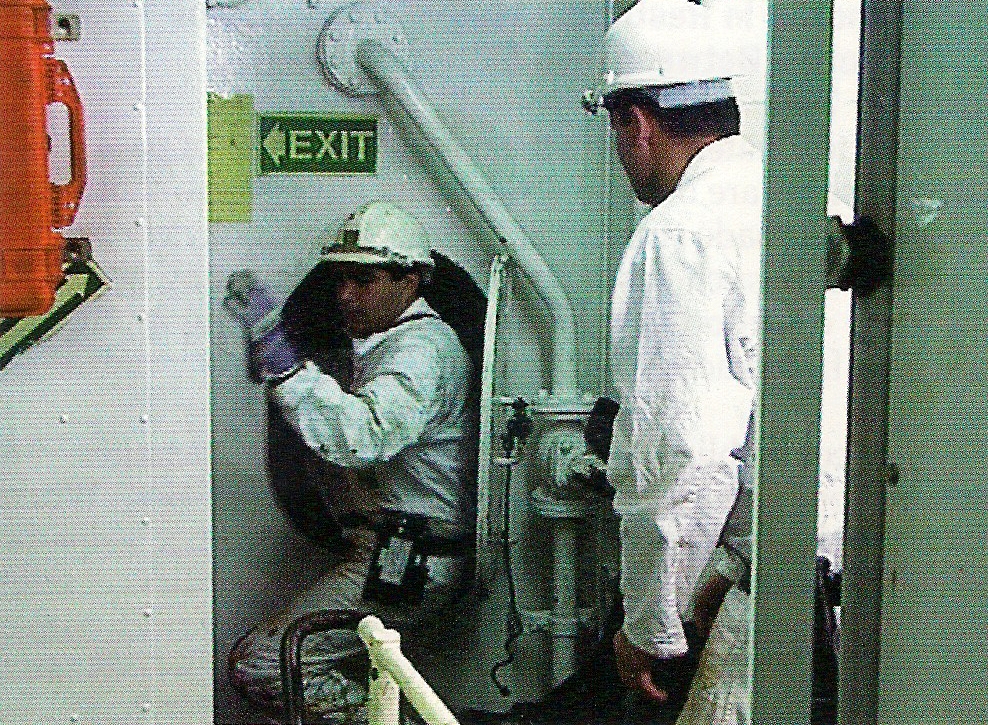
It is usually expected that the inspection will take about six to eight hours and be
performed in the following order -unless the inspection should be altered to better
suit the vessel´s schedule:
1. Review of documentation (preparatory for opening meeting).
2. Opening meeting with Master, Chief Engineer and Chief Mate (if available).
3. Complete review of the documentation.
4. Wheelhouse and navigation.
5. Communications (radio room or GMDSS satation).
6. The exterior of the wheelhouse.
7. The exterior of the accommodations to the poop.
8. Up the main deck to the forecastle and forecastle spaces.
9. Back down the main deck and checking a ballast tank (as agreed in the
opening meeting).
10. The Pump Room to the Cargo Control Room with the Chief Officer.
11. Discussion with Chief Engineer and into the Engine Room, including
review of PMS.
12. With the Master back through the internal areas of the accommodations.
13. Finally, a period for the inspector to summarize his thoughts.
14. A final meeting with the Master and department heads.
Variations in scheduling will be considered if they are necessary to avoid disruption of
the ship´s normal operation. As well, the order of inspection can be varied as necessary.
During the final meeting, a list of observations is reviewed with the Master. This review
ensures that all observations are based on the correct information, and no
misunderstanding occurs. The Master is not expected to provide corrective actions or
imply agreement with the observations - his signature is only an indication that he has
received the observations.
To contact us:
INTERNATIONAL SHIP´S REGISTER, S.L.
Avda. Profesor Peraza Ayala, 11-1º-3
Edificio LAS CUMBRES, "B"
38001-S/C. de Tenerife (Canary Islands) _ SPAIN
Phone: +34 922 270616 / +34 609 930983 (24 hrs.)
Fax: +34 922 270616
LINKS